To the inexperienced, line testing is really simple or it would be if the statements below were correct – but not one is correct.
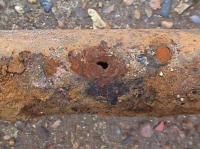
Line Myths
- Suction lines cannot leak because holes cause a loss of prime.
- Suction lines cannot leak because they run at sub-barometric pressure.
- Holes in vent lines aren’t a problem.
- Constant pressure during a pressure or vacuum test implies no holes.
- A fall in pressure indicates a leak.
- Testing a line requires access to both ends of it.
- SIR can identify line leaks, as they are proportional to sales.
Solutions
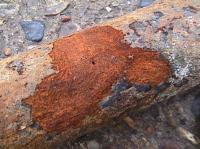
Given the above weaknesses, systems of testing have to be devised to overcome these difficulties and no one solution is applicable in all cases. MassTech International engineers and scientists therefore devised a suit of US EPA certified protocols allowing their franchisees to choose technologies appropriate to the scenario.
Usually, pressure in a tight line increases with time, a fact which negates ‘constant pressure’ as a criterion for passing a line. MassTech International Ltd had already solved this problem for ullage space testing and were able to transfer this compensation technology to a line leakage test. Generally the line is tested at more than one pressure and all pressure tests are monitored for temperature. Pressure may be positive or negative (vacuum), the choice being dependent on the presence of pressure relief or flow control valves or on fuel level into which the line may happen to start/end. Pass/fail criteria vary according to whether the line is full or empty.
Corroded Underground pipe MassTech line test analyses normally include a ‘measure’ of leak rate but these leak rates should be used with caution – for example, a leaking suction line usually only puts fuel into the ground when it is not being used and this makes it difficult to calculate losses under real operational conditions. When test pressures are applied, they are applied using an ‘inert’ or ‘safe’ gas. These can be dosed to provide leak location information although caution should be exercised as to the usefulness of such information. Repair of a section of line can often lead to accelerated failure of the line in the future due to galvanic effects.
Line failures are easily the most common source of non-criminal loss of gasoline and diesel at gas stations and, fortunately, they are the simplest and cheapest to fix. It is the cost of fuel contamination to the environment and the loss of product at ‘pump prices’ that are the downside of these arguments. Many think line leakage testing is easy. It is if for those who have no knowledge of the difficulties and anomalies involved. Client companies who use expert advice are unlikely to be bothered by environmental or regulatory retaliation – they will be doing what is best for themselves and for the environment and being seen to be doing the best. The safest approach is to choose a vendor whose line tests are certified to US EPA protocols.
Pipeline Testing

Pipeline testing is often the most difficult of all integrity testing depending on the complexity and scale of the installation. The normal method of continuous monitoring is by differential flow measurement but it is not considered a very sensitive technique. Long fully buried lines behave like long thin tanks while lines of less than 200 litres can be tested using conventional line testing methods. For all other lines, tests need tailoring according to circumstances
MassTech International have a standard questionnaire which will allow us to advise you how best to tackle the problem. It covers: the use of the line; its material dimensions and construction, its geography and variations along the line; its Instrumentation and monitoring; possible additional loss detection and location; environmental and commercial risks