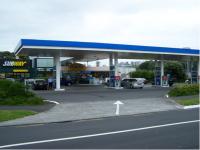
MassTech is not one tank test technology but a suite of more than a dozen, each with its own application and strength. Each technology is third party certified to US EPA, most to better than 0.38 lt/hr. The most important are NWG (US EPA) listed, an honour not normally accorded to non-USA methods. The latest certifications are for volumetric high precision tests and are among the most accurate and sensitive in the world.
To test a tank and line system fully requires more than one technology and the normal MassTech protocols run these tests concurrently. The technician on site makes a decision on the most useful test strategy by comparing the client’s requirement for the test, the client’s operational needs and the situation on the site. Where either of the operational needs and the situation on site conflict with the needs of the test, the client needs to be guided but ultimately will make the decision on test strategy having been advised of the implications.
Motives for Testing
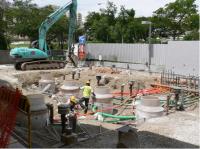
Tanks are tested to confirm their health or to explain and diagnose problems. In the case of confirming health, tests are normally conducted: prior to commissioning, on change of responsibility or on particular birthdays of either the tank or of the installation or of the site licence. MassTech uses a protocol called Pascal Perfect for the first two of these requirements so that installation or maintenance faults are picked up before the owner takes on the onerous responsibility of running the site.
Where tests are used to diagnose faults, the type of suspected fault should guide the test protocol. Faults may be suspected in the face of the following evidence:
- Fuel can be smelled or seen, on or off the site. Locations may include the forecourt surface, man-chambers, drains and watercourses. This evidence provides a good indication that there is, or has been, a problem but is a poor indication as to the source of the problem.
- Reconciliation records, systems or technologies show apparent losses.
- Adjacent inventory measurements over periods of zero sales show apparent losses, often associated with deliveries.
- Vehicle breakdowns, emulsion in pump filters, inventory gains; water paste or other water measurement systems indicate water ingress.
Situations which can cause problems for tank testers

- The pressure of groundwater nearly or exactly balances the hydrostatic pressure of the fuel at the leak site. MassTech overcomes this by testing the tank either at two different levels or at two different ullage pressures, back to back. This strategy results in different apparent loss of gain rates, whose comparison can help with diagnosis and even to location of faults.
- The tank is nearly full or is overfilled. Since tanks are rarely installed exactly horizontal, the high end of the tank entraps vapour whose expansion or contraction during the test causes erroneous results. Fuel should be sold or removed until the level is no more than 92% of the tank diameter.
- The client imposes conditions on the test that place its result in jeopardy. The client may not allow the tank to be closed for sufficient time in which case the regulatory leak threshold may not be achievable, however a valid result may still be possible at a higher leak rate threshold.
- There is no access to the ullage space to vent it for mass readings or to pressurise it. A MassTech acoustic test may be possible but it will not cover all scenarios. Vent access is required for all known full system tests, whether MassTech or not. MassTech technical staff should be consulted under such situations.
- The capacity or diameter of the tank is unknown. MassTech, uniquely, has the ability to measure the dimensions of a tank from the fill pipe or suction line but even if this is not done, a result may be achievable within the limitation of certain assumptions.
The Ideal Test
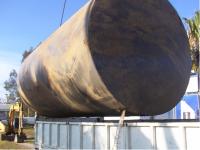
For the tank itself, the test protocol which provides the most secure result is as follows:
The tank is free vented for long enough that the ullage pressure is at barometric. Two or three sets of mass readings sandwiched between atmospheric readings are taken. The tank is sealed and pressure recorded every 10 seconds for 25 minutes.
The tank is free vented again for long enough that the ullage pressure is at barometric. Two or three sets of mass readings sandwiched between atmospheric readings are taken. The tank is sealed, pressurised with nitrogen to 10 kPa above barometric pressure and the pressure recorded every 10 seconds for between 25 minutes and 2 hours according to ullage volume.
The tank is free vented again for long enough that the ullage pressure is at barometric. Two or three sets of mass readings sandwiched between atmospheric readings are taken.
There are circumstances where parts of this test can be shortened or even excluded but these are rare and exclusions could render the test inconclusive.
Situations which may result in an Inconclusive Result
- Mass readings were taken without the ullage space being free vented. A common error is to attempt mass readings while the vapour recovery system is still active i.e. with the PV valve still in place.
- Atmospheric readings are not recorded either side of each mass set or are fluctuating wildly.
- Data Quality Indicators exceed 3, caused by having the regulator set too high, injecting for too long, having too long a flexible line or having it obstructed or leaking, not securing the probe to the tank floor, moving the probe during the test, not injecting enough nitrogen initially or not waiting sufficiently before starting the M readings.
- Mass sets are missing or interrupted.
- There is an unauthorised withdrawal, addition or transfer of fuel etc during the test, including failure to arrest sales.
- Tank is tested too full or overfilled.
- Test is not conducted for long enough.
- Automated analysis checks on the data reveal important inconsistencies.
Situations which may result in an Incorrect Result
There has never been an incorrect result called in MassTech’s twelve years in tank testing confirming the closeness of MassTech’s EPA probability of detection (P(D)) to 100%. However unlikely or inconvenient a result may seem, it is independent, analysed by specialist experts and is valid.